Gold mining: From the beginnings to the future
Gold facts & figures Arnulf Hinkel, Finanzjournalist – 19.05.2022
The development of gold mining over the centuries and how climate change will shape the future of gold mining.
More than 205,000 tonnes of gold have been mined from the dawn of mankind to the present day, according to recent data published by the World Gold Council. In 2021 alone, this figure was 3,560.7 tonnes, which, together with recovery from scrap gold and e-waste, allowed for a gold supply of 4,666.1 tonnes on the world market. Over the past ten years, gold demand has risen almost uninterruptedly, a development this is not expected to change significantly in the foreseeable future. But where does the gold that enters the market in the shape of bullions, coins or jewellery actually come from – and how is it produced?
Most of the gold in the universe is found in outer space, where planets and small celestial bodies such as comets, asteroids and meteorites harbour extensive amounts of gold. The eggplant-shaped asteroid Eros, for example, at a length of only 34 kilometres contains no less than 20 billion tonnes of gold.
The precious metal was created by the collision of two neutron stars and, as the result of a so-called supernova core collapse, is a component of celestial bodies of all kinds, including Earth. Since the precious metal is extremely heavy, it migrated into the core of Earth during the formation of our planet, where the amount of gold it holds today would suffice to cover the entire surface of the Earth with a 45 cm thick layer. As the initially liquid Earth mass cooled, the precious metal was deposited in and on its crust. Volcanic eruptions also brought gold back to the surface.
This gold deposit is the only one that can still – and only partially – be accessed by humans today. The following paragraphs will discuss the ways in which gold can be extracted, how the methods of gold extraction have evolved over the millennia and what the future of gold production might look like.
The beginnings: gold extraction from secondary deposits
The precious metal has probably held a special fascination for mankind since the very beginnings, not only due to the brilliance of gold, but also due to the fact that it is imperishable and easily molded. The extreme rarity of the precious metal quickly led to its use in jewellery and becoming synonymous with wealth, high social status, and power.
At first, gold was not mined, but simply found in the form of nuggets – in so-called secondary deposits such as riverbeds or gold-bearing debris brought to light by erosion and weather effects. Such gold deposits are called secondary deposits, and the precious metal that is relatively easy to extract there is called placer gold or stream gold.
The oldest gold discoveries mined around 6,600 years ago
While the theory cannot be proven, our prehistoric ancestors probably already used gold. What is, however, certain is that gold played an important cultural and social role from around 4600 BC onwards, scientifically proven by the analysis of extensive gold discoveries in the burial grounds of Varna in what is now Bulgaria. The approximately 3,000 pieces of jewellery testify not only to the widespread use of gold already in the late Neolithic and early Copper Age, but also to its social significance in the hierarchies of the time. Another finding from the gold pieces of Varna is that people at the time were already processing gold that was nearly pure. Most of the examined jewellery has a purity of between 23 and 23.5 carats.
The methods of gold extraction were initially conceivably simple. With the enormous popularity of the precious metal in ancient Egypt from around 3100 BC onwards, the search for gold was professionalised and carried out on an ever larger scale.
Gold panning – the oldest form of gold mining
Anyone who has ever tried their hand at hobby gold prospecting can confirm that it is an extremely strenuous activity. Gold mining in ancient Egypt was, in fact, slave labour: thousands of slaves had to dig up rock, sand or mud in gold-bearing fields or rivers to utter exhaustion, sometimes even to the point of death. The then panned the material under running water until the gold separated from the rest of the dirt or mud in the form of nuggets.
An alternative was the use of so-called gold panning troughs, where the gold collects against horizontally placed ribs. Both gold washing techniques are physically possible only because gold is extremely heavy. For comparison: with a density of 19.3 g/cm3, gold is more than seven times heavier than marble. There are only six elements on earth that have a higher density than gold; among them is platinum.
The fact that the process of gold washing was worthwhile at all was not only because – as in Egypt – the work was often conducted by slaves. At the time, the secondary deposits of the precious metal were also still largely untouched. Over the millennia, however, they were increasingly exploited, which is why the days of the gold rush are long gone. They happened from 1848 in California, in 1886 in Witwatersand, South Africa, and at the end of the 19th century on Alaska’s Klondike River.
More elaborate but more profitable: gold extraction from primary deposits
Placer gold accounts for only a fraction of all gold deposits on earth, even if only taking into account those easily mineable from today’s perspective. The lion’s share is mined gold, extracted from gold-bearing ore in mines. This technique of gold extraction, which is much more complex than gold panning, has been in practise since the Bronze Age, i.e. for about 5,000 years, as evidenced by the discovery of a gold mine in Sakdrissi, Georgia, in 2004.
Because of its very low reactivity with other substances, it was difficult to isolate the mountain gold that is firmly embedded in the ore, requiring the mined ore to be laboriously crushed as much as possible to dissolve the gold from it. But even with finely ground ore, gold washing was not an effective method of separating the gold from the rock.
Already in antiquity, in the period from about 800 BC to 600 AD, much more efficient methods of extracting gold were developed. The development of more efficient – and in the last decades also increasingly more environmentally friendly – concepts of gold mining are therefore ongoing.
1. The amalgam process
In the middle of the 14th century, the amalgam process was introduced for gold mining and is now rarely used. In this gold extraction process, mined gold ores or gold mud are enriched with mercury. The resulting amalgam is liquid and thus automatically separates from the rest of the mined ore. The isolated amalgam is heated, leaving behind the pure precious metal due to the much lower boiling point of mercury compared to gold.
The problem with this method is the release of the highly toxic mercury vapours, which pose a great danger to humans and the environment. The amalgam process was therefore replaced some time ago by less harmful gold extraction methods and is now only used in the Amazon region.
2. Cyanide leaching
The cyanide leaching process requires several steps. First, the extracted gold-bearing ore is ground into very fine sand, which is mixed with a sodium cyanide solution to dissolve the gold from the ore sand together with the used leach. The gold-cyanide leach mixture thus is separated in the next step with the help of zinc dust. The isolated raw gold is then refined to be further processed to fine gold.
Cyanide leaching allows for a higher gold yield than the amalgam process. If used correctly, it causes less pollution to the environment, but technical accidents can lead to the release of the highly toxic leach and, in the worst case, an environmental disaster, as seen 22 years ago when the Baia Mare dam broke in Romania. In addition, cyanide leaching can easily produce hydrocyanic acid, which is extremely toxic to humans and the environment. The method is still applied today under the strictest safety protocols, especially in mining areas with a particularly high gold content.
3. The anode slime process
The anode slime process works entirely without toxic substances and is particularly effective in the extraction of gold as a by-product when mining other precious metals such as copper or tin. In the process, based on an electrochemical approach, gold is separated from the other metals via electrolysis. The gold migrates together with the other precious metals in the form of anode sludge from one electrode to the other, aided by strong electrical current. The individual precious metals can then be separated from each other.
The high energy consumption is the only disadvantage of this most common method of gold extraction today. It is more effective than the amalgam process and cyanide leaching. Moreover, the anode slime process does not endanger human health or the environment. The process is also widely used to recycle scrap gold.
4. The borax process
Another environmentally friendly, but significantly less energy-intensive method of gold extraction is the borax process. By adding borax, also called sodium borate, the melting point of gold is greatly reduced. The low melting point of the gold-bearing ore mass allows the use of cheaper, but also less powerful heat sources. The gold settles at the bottom of the crucible during the melting process, while rock materials such as ore, silicon, quartz, as well as all oxides rise to the top. The borax process not only saves energy, it is also an excellent method for the recovery of fine gold.
5. The Miller process
With a share of about 70 per cent, the Miller process, patented in 1867, is the most widely used refining method for extracting fine gold from raw gold. In this chemical process, a stream of pure chlorine gas is blown through a crucible filled with molten but impure gold. The process purifies the gold to a degree of 99.999 per cent, as almost all other elements contained in the raw gold form chlorides earlier than gold, salts which can be removed relatively easily.
Recycling: increasingly relevant for gold extraction
According to the 2021 annual report of the United States Geological Survey, around 54,000 tonnes of gold remain in the earth worldwide that can be mined at reasonable cost at today’s technology and research standard. Completely new, recoverable gold deposits have not been discovered for many years. Based on the annual production volume of 2021, these 54,000 tonnes would be used up in a good 15 years.
This is not the only reason why gold recycling is becoming increasingly important: Recovery from scrap gold is much cheaper and environmentally friendly than mining gold. Even with state-of-the-art technology and procedures, the classic production of one kilo of gold releases between 12 and 16 tonnes of carbon, whereas recycling scrap gold from jewellery or coins only produces 53 kilos, less than one-twentieth.
The share of recycled gold in the total annual production currently amounts to about 28 per cent and is strongly dependent on the latest gold price: The higher it is, the more likely people are to part with their old gold jewellery – especially in emerging countries. Today, the recycling rate for old gold is already 100 per cent. However, gold recovery from electronic scrap, e.g. from smartphones, PCs, or motor vehicles holds enormous growth potential.
The future of gold recovery: optimising carbon footprint
Most people have realised that only with the efforts of each individual do we stand a chance to mitigate the impending climate catastrophe. This is especially true for industries that leave a large ecological footprint, including the gold industry, which sees itself under obligation on the one hand through regulatory measures on the part of alliances by committed states, and on the other hand through its end customers. Environmentally conscious consumers seek to buy jewellery from recycled gold, while institutional and private investors aim to contribute to a better climate balance through the conscious compilation of their investment portfolio.
There are basically two ways to achieve more environmentally and climate-friendly gold extraction: firstly, the use of mining methods that are less polluting and energy-intensive than those commonly used today. One recent promising approach is the replacement of highly toxic hydrocyanic acid with harmless chlorine compounds in mining. This innovative process also promises an up to 20 per cent more efficient gold extraction.
On the other hand – and this is by far the more forward-looking way – carbon emissions can be significantly reduced by intensifying gold recovery from electronic scrap, so-called urban mining. The company Umicore, exclusive supplier of the gold bars deposited as collateral for Xetra-Gold bearer bonds, produces up to 100 tonnes of gold bars annually from scrap gold and electronic waste. To date, the globally active materials technology and recycling company has been able to save more than 1 million tonnes of CO2 compared to mine production. Urban mining need not be exclusive to high-tech corporations, as is demonstrated by the Earthbeat Foundation initiative. Amongst other projects, it supports micro-producers of gold in the implementation of urban mining.
In the future, it will be possible to extract gold from electronic waste in an even more climate-friendly way. A new technology currently being developed is based on the use of bacteria and will allow for urban mining in a more cost-effective way, without the use of chemicals and nearly carbon free.
While it will likely never be possible to achieve climate neutrality in gold production, there are numerous promising approaches to minimising its ecological footprint.
Xetra-Gold Hotline
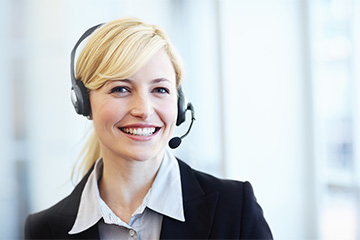
Do you have questions? We have the answers. Contact us here: 9 a.m.–6 p.m. CET
xetra-gold(at)deutsche-boerse.com
For press inquiries: media-relations(at)deutsche-boerse.com